技術紹介
成形の強み
プラスチックの可能性を拓く多彩な成形加工技術を確立
タカギセイコーは、プラスチック製品の高精度化・高機能化要求に応え、中長期的視点から新しい加工技術の開発や実用化に取り組んでいます。
他社の追随を許さない成形法のバリエーションは、製品の市場競争力を高め、プラスチックの新たな可能性を拓くリソースとして機能します。
1射出成形
-
バンパー -
携帯電話部品 -
MCF成形(超微細発泡成形)
大型から精密な小型・超薄肉製品まで、高速で量産
樹脂を加熱・溶融して金型内に高圧で射出注入し、金型内で冷却・固化して成形する加工法です。デザインの自由度が高く、複雑な形状の成形品も精密に成形でき、しかも高速量産が可能なため、車両のバンパーのような大型製品からスマートフォン筐体のような小型精密製品まで幅広く活用されています。
2DCP-RIM
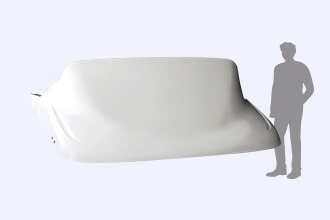
デザイン性や強靭性を求められる乗用車や住宅など超大型製品
1989年に、トラックのエアデフ・ハイルーフなどの超大型製品を成形できる日本初のDCP-RIM法を開発しています。この成形法は、2種類の液体を混合して金型内に注入し、化学反応を利用して成形する加工法です。サーマルリサイクルに対応するDCP樹脂(ジシクロペンタジエン)を活用し、複雑なフォルムの厚肉大型品の軽量化を実現する成形法は、多品種少量生産を支えます。
3回転成形
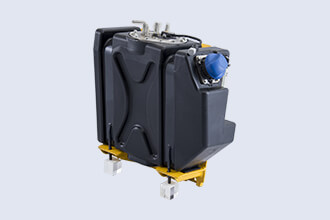
複雑なフォルムの部品を一体成形し、剛性、機密性が高い
中空状の金型に粉末樹脂を投入し、金型を回転させながら加熱・冷却する加工法で、複雑なフォルムの成形に最適です。耐衝撃性、気密性、均一性に優れた技術を確立する当社は、2012年からディーゼルエンジン車用尿素水タンクの生産を開始しているほか、 様々なタンクの生産に対応しています。
4押出成形
パイプなど断面が同一形状の製品に適す
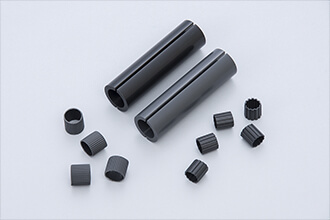
5ブロー成形
機能性と高外観性を追求する異形ブロー製品
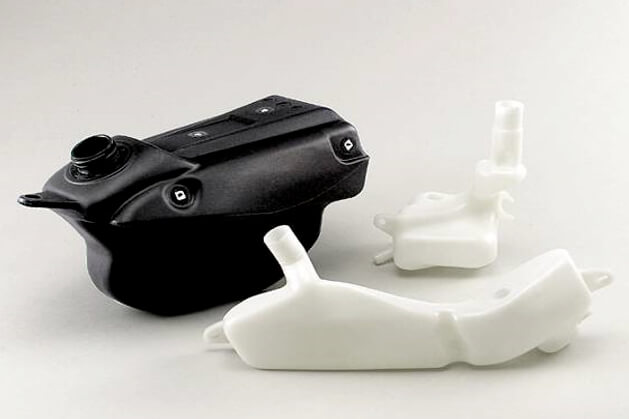